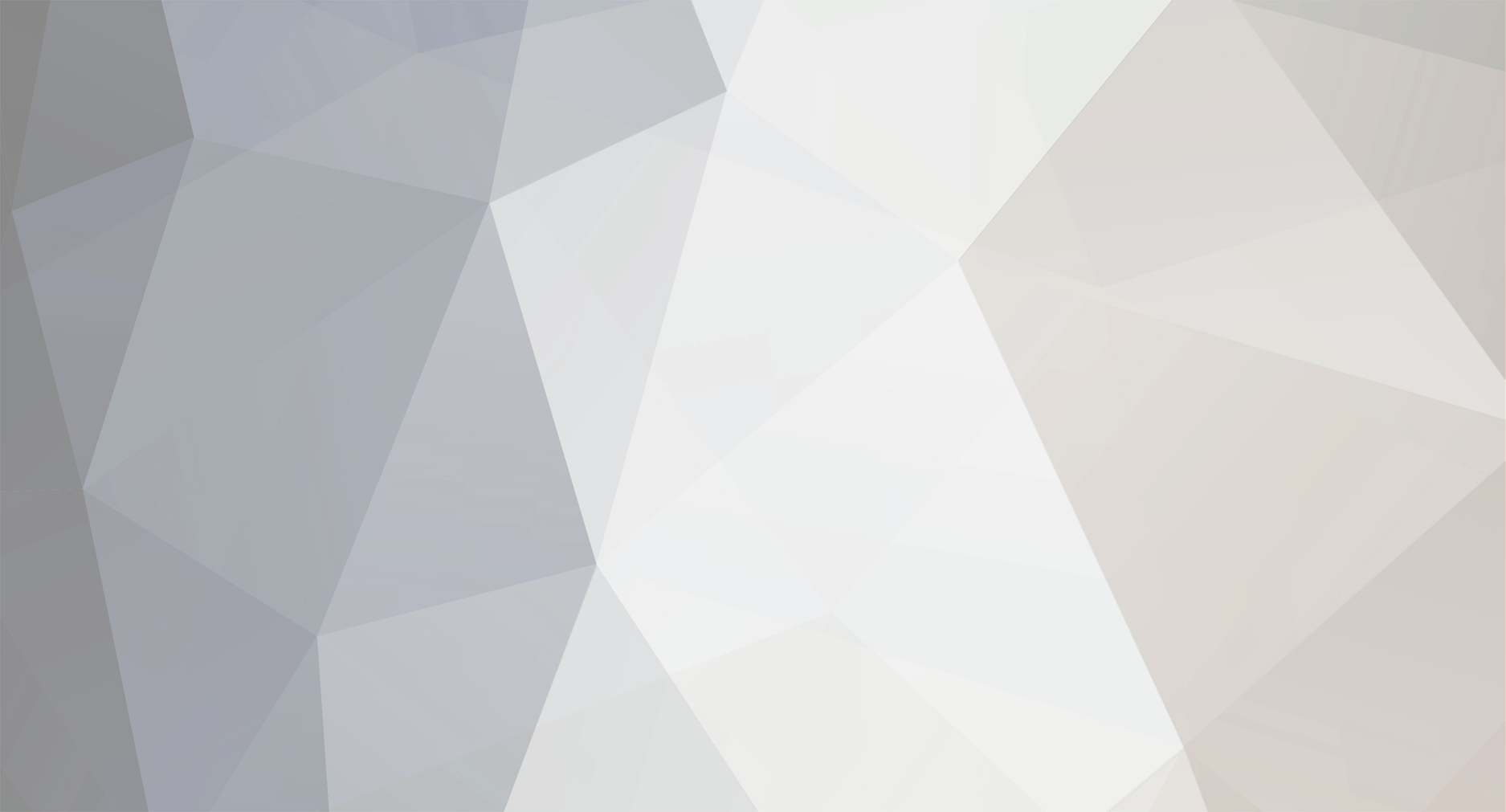
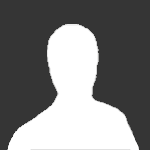
leizuofa
Staff group-
Content Count
198 -
Joined
-
Last visited
Community Reputation
0 Neutral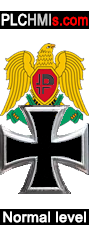
About leizuofa

-
Rank
Intermediate PLC Programming Learner - 1
-
SIEMENS-RU Что такое версия прошивки ПЛК? – Аппаратное обеспечение ПЛК Сименс
leizuofa posted A plc and hmi russian article in PLC programming learning
В этой статье мы поговорим о серьезной проблеме, которая часто возникает, когда вы начинаете программировать свой ПЛК, это распространенные ошибки версии прошивки и способы их устранения. Содержание: Какова версия прошивки ПЛК? Почему версия прошивки может вызывать проблемы? Как узнать версию прошивки аппаратного ПЛК? Как устранять ошибки версии прошивки? Выводы. Какая версия прошивки ПЛК? Прошивка ПЛК или модуля ПЛК (вводы-выводы, модули связи и т. д.) — это просто внутреннее программное обеспечение, установленное в ПЛК, которое отвечает за то, что на самом деле может делать оборудование. Версия прошивки определяет, какие внутренние функции есть у вашего ПЛК, такие как протоколы безопасности, внутренние функции оптимизации, лучшая обработка времени и другие различные функции и возможности. ПЛК со старой версией прошивки будет иметь меньше функций и внутренних возможностей, чем ПЛК с новой версией прошивки. На рисунках 1 и 2 показано, как один и тот же аппаратный ПЛК будет иметь разные функции и возможности производительности с разными установленными версиями прошивки. Рисунок 1 – Версия прошивки V4.0 Рисунок 2 – Версия прошивки V4.4 Вы заметили, что тот же самый ЦП теперь имеет больше функций, добавленных просто путем обновления до более высокой версии прошивки? С более высокой версией прошивки V4.4 ЦП теперь имеет OPC UA среди других функций, добавленных к его возможностям производительности. Почему версия прошивки может вызывать проблемы? Смотрите, вы обычно начинаете свой проект ПЛК, выбирая ПЛК, а затем начинаете программирование. Вы выбираете свой ПЛК в TIA Portal в соответствии с одним из двух пунктов: Вы уже приобрели аппаратный ПЛК, поэтому вы выбираете тот же ПЛК, который у вас фактически есть в проекте TIA Portal. Вы все еще не приобрели ПЛК, поэтому вы выберете ПЛК в TIA Portal, который соответствует вашим требованиям, а затем купите его позже. В любом из двух случаев, если версия прошивки ПЛК, выбранная в проекте TIA Portal, отличается от версии прошивки фактического оборудования, у вас возникнут проблемы. И ваша программа даже не будет загружена в аппаратный ПЛК. Поэтому вы всегда должны следить за тем, чтобы версия прошивки фактического ПЛК соответствовала ПЛК, выбранному в TIA Portal. Стоит отметить, что если версия прошивки, выбранная в TIA Portal, старше фактического ПЛК, у вас не возникнет никаких проблем с вашей программой, вы потеряете некоторые функции и возможности ПЛК, но ваша программа будет работать нормально. Проблемы возникнут, если верно обратное, если версия прошивки, выбранная в TIA Portal, новее фактического ПЛК, у вас возникнут проблемы. Вот почему, если вы не знаете версию прошивки вашего оборудования, вам следует выбрать более старую версию в проекте TIA Portal. Как узнать версию прошивки аппаратного ПЛК? Мы можем узнать версию прошивки аппаратного ПЛК, которая у нас есть, одним из двух способов: Из самого ПЛК Версия прошивки любого модуля ПЛК всегда записана где-то на аппаратном устройстве. Смотрите следующие рисунки. Рисунок 3 — Версия прошивки FS:04 Рисунок 4 — Версия прошивки V7.0.5 Из программного обеспечения TIA Portal Используя программное обеспечение TIA Portal, вы можете подключить свой ПЛК к своему TIA Portal и выполнить поиск устройства, затем вы можете найти версию прошивки аппаратного устройства, см. следующие шаги. Вам даже не нужно создавать новый проект; Достаточно только вида проекта TIA Portal, см. рисунок 5. Рисунок 5 – Вид проекта TIA Portal без создания проекта. Из онлайн-доступа найдите свой ПЛК. Поскольку соединение между TIA Portal и ПЛК осуществляется через кабель Ethernet, мы будем использовать опцию подключения Ethernet. Дважды щелкните на обновлении доступных устройств, чтобы начать поиск вашего ПЛК. См. рисунок 6. Рисунок 6 – Обновление доступных устройств для поиска вашего ПЛК. Если есть соединение между ПЛК и TIA Portal, то программное обеспечение должно найти ваш ПЛК. См. рисунок 7. Рисунок 7 – Ваш ПЛК был найден программным обеспечением. Теперь дважды щелкните на Онлайн и диагностика, чтобы отобразить информацию о вашем ПЛК. См. рисунок 8. Рисунок 8 – Онлайн-информация о ПЛК. Из атрибута General вы можете узнать версию прошивки вашего ПЛК, как показано на предыдущем рисунке. Вы также можете узнать версию прошивки из атрибута Functions. См. рисунок 9. Рисунок 9 – Версия прошивки из атрибута functions. Как обрабатывать ошибки версии прошивки? Сначала давайте создадим сценарий ошибки версии прошивки, а затем посмотрим, как обрабатывать и исправлять эту ошибку. Начнем с создания нового проекта, а затем добавим новое устройство. В этом примере ПЛК мы намеренно выберем более новую версию прошивки, чем у фактического аппаратного ПЛК. Мы знаем, что прошивка нашего ПЛК — V4.0, но в TIA Portal мы выберем версию прошивки V4.4. Смотрите рисунок 10. Рисунок 10 — Добавьте новый ПЛК с более высокой версией прошивки. Нажмите OK, чтобы добавить свое устройство, и все, вы создали ситуацию, которая вызовет ошибку прошивки. Чтобы это увидеть, давайте попробуем загрузить проект в наш ПЛК. Обратите внимание, что мы даже не написали никакого кода. Просто загрузите его в ПЛК. Смотрите рисунок 11. Рисунок 11 — Загрузка в ПЛК не удалась, несовместимая прошивка. Как вы видите на предыдущем рисунке, как только вы попытаетесь загрузить проект в ПЛК, появится ошибка о том, что версии прошивки ПЛК и TIA Portal не совпадают. Вы даже можете увидеть это, если попытаетесь выйти в Интернет. Смотрите рисунок 12. Рисунок 12 — ПЛК находится в состоянии ошибки. Чтобы устранить эту ошибку, нам просто нужно изменить версию прошивки ПЛК, выбранную в проекте TIA Portal, на более старую или ту же версию прошивки, что и у фактического аппаратного ПЛК. Для этого мы переходим на страницу свойств ПЛК и выбираем Изменить версию прошивки в атрибуте Общие. Смотрите рисунок 13. Рисунок 13 — Параметр Изменить версию прошивки. После нажатия кнопки Изменить версию прошивки появится окно изменения устройства; в этом окне вы сможете изменить версию прошивки. См. рисунок 14. Рисунок 14 – Окно изменения устройства. В окне изменения устройства вы увидите текущее устройство, которое вы выбрали ранее, и новое устройство, прошивку которого вам нужно сопоставить с той, что у вас есть на самом деле. Обратите внимание, что при выборе более низкой прошивки, например V4.3, информация в нижней части окна покажет вам, какие функции вы потеряли при переходе на более низкую прошивку, как вы видите на предыдущем рисунке. Теперь измените прошивку нового устройства на версию V4.0 аппаратного ПЛК. И обратите внимание, сколько функций и возможностей ПЛК потерял, просто выбрав более низкую прошивку. См. рисунок 15. Рисунок 15 – Сопоставление прошивки между аппаратным ПЛК и программным обеспечением. Нажмите OK, чтобы подтвердить изменения, и теперь попробуйте снова загрузить свой проект в ПЛК. Вы заметите, что теперь проект будет загружен в ПЛК без каких-либо ошибок. См. рисунок 16. Рисунок 16 – Проект загружен в ПЛК. Успешная загрузка проекта в ПЛК означает, что ошибка версии прошивки теперь исправлена. Вы также можете выйти в Интернет и проверить это из онлайн-просмотра проекта ПЛК. См. рисунок 17. Рисунок 17 – Онлайн-просмотр проекта. Зеленые галочки и круги, которые вы видите на предыдущем рисунке, указывают на то, что все конфигурации программного обеспечения и оборудования совпадают и совместимы друг с другом. Заключение Ошибки версии прошивки – очень распространенная проблема, с которой можно столкнуться при создании нового проекта в TIA Portal. Лучше всего знать версию прошивки имеющегося у вас аппаратного устройства и сопоставить ее с прошивкой выбранного устройства в TIA Portal. Если вы не знаете прошивку аппаратного устройства, то вам следует выбрать самую старую версию выбранного модуля в TIA Portal. Чтобы избежать проблем с прошивкой вашего проекта. -
SIEMENS-RU Использование битов памяти тактовых импульсов в TIA Portal – Сименс PLC
leizuofa posted A plc and hmi russian article in PLC programming learning
В этой статье мы рассмотрим биты памяти тактовых импульсов в TIA Portal и Siemens PLC. И покажем, как включить использование битов памяти и как это может помочь вам избежать кодирования большого количества логических линий для получения простой функции, которую ваш ПЛК уже выполняет внутри. Содержание: Что такое биты памяти тактовых импульсов? Необходимость в битах памяти тактовых импульсов. Включение памяти тактовых импульсов в моем проекте. Простой пример программы. Моделирование программы. Заключение. Что такое биты памяти тактовых импульсов? Память тактовых импульсов – это битовая память, которая периодически изменяет свой двоичный статус в соотношении 1:1. Это просто означает, что она периодически изменяет свой статус между истинным и ложным с предопределенной частотой. В ЦП предварительно определены 8 бит памяти тактовых импульсов, поэтому их также называют байтами памяти тактовых импульсов. Вы решаете, какой байт памяти ЦП станет байтом памяти тактовых импульсов, когда вы включаете использование байта памяти и назначаете параметры памяти тактовых импульсов. Необходимость в битах памяти часов Вам не обязательно нужна память часов, так как вы можете создать свою собственную логику и достичь той же функциональности. Тем не менее, ее полезно иметь в кармане, когда вам понадобится такая функциональность. Так как создание 8 отдельных логических схем для 8 бит памяти часов займет некоторое время и усилия и может сделать вашу программу неоправданно большой. Вы можете использовать память часов, например, для активации мигающих индикаторных ламп или для инициирования периодически повторяющихся операций, таких как запись фактических значений. Каждому биту байта памяти битов часов назначается частота. См. следующую таблицу. Бит байта памяти часов 7 6 5 4 3 2 1 0 Период (с) 2.0 1.6 1.0 0.8 0.5 0.4 0.2 0.1 Частота (Гц) 0.5 0.625 1 1.25 2 2.5 5 10 Таблица 1. Частоты битов памяти часов согласно справочному руководству TIA Portal. Включение памяти часов в ПЛК Siemens Чтобы использовать биты памяти часов в вашей логике, вам необходимо включить использование байта памяти часов в свойствах ЦП. См. рисунок 1. Рисунок 1 — Включение использования байта памяти часов Вы можете выбрать адрес байта, который вы хотите назначить для памяти часов, просто убедитесь, что он не конфликтует с другими байтами памяти в логике вашего ПЛК. Как вы видите на рисунке, мы выбрали адрес 0, поэтому, если вам нужно использовать бит синхронизации 2 Гц, вы будете использовать бит %M0.3 Пример программы конвейерной ленты Tia Portal В предыдущей статье мы использовали простой пример конвейерной ленты, перемещающей продукт между началом и концом ленты. Был светодиод индикации, который включается, когда лента работает. Смотрите рисунок 2. Рисунок 2 — Простая система конвейерной ленты Мы будем использовать тот же пример, но на этот раз мы сделаем светодиод более интуитивно понятным, используя биты памяти часов. На этот раз мы будем использовать биты памяти часов со светодиодом, чтобы дать индикацию различных случаев процесса. Описание процесса В системе конвейерной ленты, управляемой ПЛК, на двух концах ленты есть два датчика присутствия для обнаружения наличия продукта. Когда продукт обнаружен в начале ленты, конвейер можно запустить с помощью кнопки запуска, а когда продукт достигает конца, лента автоматически остановится и не будет работать снова, пока новый продукт не будет обнаружен снова в начале и не будет нажата кнопка ПУСК. Светодиод индикации должен иметь более одного поведения в зависимости от текущего случая системы. Эти случаи следующие: Если в начале ленты есть продукт, но кнопка ПУСК еще не нажата, светодиод должен мигать с частотой 0,5 Гц. Если конвейер перемещает продукт, светодиод должен мигать с частотой 2 Гц. Когда продукт достигает конца ленты, светодиод должен загореться. Когда продукт удаляется с конца, светодиод выключается. Проект IO У нас есть 4 цифровых входа, как показано ниже: START: кнопка запуска для запуска конвейера. STOP: кнопка остановки для остановки конвейера в любой момент. P1: датчик присутствия в начале ленты. P2: датчик присутствия в конце ленты. У нас также есть 2 цифровых выхода, как показано ниже: MOTOR: при активации конвейерная лента начнет работать. LED: будет активирован в соответствии с последовательностью, упомянутой ранее. Программный код Сначала мы выбираем наш ПЛК и назначаем теги IO. Смотрите рисунок 3 Рисунок 3 — Назначение тегов входов и выходов Не забудьте включить использование байта памяти часов, как показано на рисунке 1. У нас будет две сети кода, одна для управления лентой конвейера, а другая для светодиодной логики. Смотрите рисунки 4 и 5 для логики. Рисунок 4 – Логика управления конвейерной лентой Рисунок 5 – Логика управления светодиодом Как вы видите, использование битов памяти часов сделало логику простой и легкой для чтения. Представьте, если бы вы создали ту же логику без использования этих битов, вы бы использовали много таймеров, и ваша логика была бы довольно сложной. Моделирование программы Ранее мы объясняли, как использовать PLCSim для моделирования нашего кода. В этом примере мы будем использовать последовательность моделирования для создания той же последовательности фактического процесса и посмотрим, будет ли поведение светодиода соответствовать предполагаемой функциональности или нет. Начните с компиляции нашего кода и запуска новой симуляции. Смотрите рисунок 6. Рисунок 6 – Программная симуляция Как вы можете видеть, светодиод теперь выключен; в начале или конце конвейера нет продуктов. Мы создали последовательность моделирования и посмотрим, как светодиод будет реагировать на различные условия процесса. Смотрите следующую анимацию. Посмотрите, сможете ли вы заметить, как поведение светодиода меняется при различных условиях процесса. Заключение Биты тактовой памяти включаются и выключаются с предопределенной частотой. Они очень полезны, когда вам нужно активировать мигающие индикаторные лампы или инициировать периодически повторяющиеся операции. Использование битов тактовой памяти сэкономит вам время и усилия, затрачиваемые на получение той же функциональности посредством вашей собственной логики. -
Что такое аналоговые входы? – Обработка аналоговых сигналов в ПЛК
leizuofa posted A plc and hmi russian article in PLC programming learning
В этой статье мы поговорим об обработке аналоговых входных сигналов в ПЛК и о том, как мы можем обрабатывать эти сигналы в процессе автоматизации. Содержание: Что такое аналоговые входные сигналы? Обработка аналоговых входных сигналов в S7-1200 и 1500. Обработка аналоговых входных сигналов в S7-300 и 400. Что лучше всего подходит для управления? – аналоговые или цифровые сигналы Заключение. Что такое аналоговые входные сигналы? Прежде чем мы углубимся в обработку аналоговых входных сигналов в TIA Portal, давайте сначала разберемся с аналоговыми входами. Любой системе автоматизации нужны входные сигналы для понимания состояния процесса, чтобы иметь возможность принимать решения, которые будут поддерживать его работу и стабильность. Эти входные сигналы являются либо дискретными, либо цифровыми входными сигналами, которые имеют форму значений 0 или 1. Другой тип входа – аналоговые сигналы. Аналоговый сигнал — это просто непрерывное представление физической величины в вашей системе, поэтому, если вам нужно контролировать температуру или давление в вашем процессе, аналоговый сигнал даст вам непрерывные и мгновенные значения, которые соответствуют реальным изменениям физической величины. Аналоговые сигналы предоставляются во многих стандартных формах, но чаще всего это 0–10 В или 4–20 мА. Это будет зависеть от типа используемого вами аналогового датчика, а также от типа аналогового модуля ПЛК, который вы можете использовать. Предположим, что аналоговый датчик давления имеет диапазон измерения 0–10 бар и выход в форме 4–20 мА. Обычно аналоговый сигнал будет иметь линейную зависимость между измеренной физической величиной и соответствующим выходом. Это означает, что если датчик измеряет 0 бар, он выдаст сигнал 4 мА, а если он измеряет 10 бар, он выдаст сигнал 20 мА, и то же самое между ними также будет линейным. См. рисунок 1. Рисунок 1 – Аналоговое представление сигнала. ПЛК по-прежнему не может понять 4-20 мА физической величины, и здесь вступает в дело аналоговый модуль ПЛК. Аналоговый модуль выполнит еще одно преобразование этого представления, чтобы ПЛК мог его фактически понять. Аналоговый модуль преобразует аналоговые измерения мА в цифровые значения, которые зависят от типа модуля, но для ПЛК Siemens эти значения всегда находятся в диапазоне 0 – 27648. Таким образом, если датчик измеряет 0 бар, выходной сигнал будет равен 4 мА, и он будет преобразован в 0-е значение внутри ПЛК. См. рисунок 2. Рисунок 2 – Аналогово-цифровое преобразование входного сигнала ПЛК затем преобразует значения 0-27648 в эквивалентное физическое измерение в зависимости от вашего программирования, к которому мы вернемся позже. См. рисунок 3. Рисунок 3 – Масштабированное измеренное значение внутри ПЛК. Аналоговая обработка температур совершенно иная, поскольку поведение датчика температуры с физическими изменениями не линейно, как у датчика уровня или давления. Вот почему существуют стандартизированные таблицы для различных типов датчиков температуры, которые сообщают, какая температура соответствует какому значению датчика. Вот почему при измерении температуры вы должны выбрать специальные типы входных модулей вашего ПЛК, где эти стандартные таблицы определены внутри, и вы напрямую получаете значение температуры, соответствующее измерению датчика. Вот почему вы не можете найти датчик температуры, на котором написан диапазон измерения напряжения или тока. Вы найдете только написанный тип датчика, например, PT100, PT1000, KTY84, PTC и т. д. Обработка аналогового ввода в S7-1200 и 1500 Чтобы увидеть, как мы обрабатываем аналоговые сигналы в современных ПЛК семейства S7, давайте начнем с создания нового проекта и добавления ЦП S7-1200. Мы также добавим модуль аналогового ввода/вывода. См. рисунок 4. Рисунок 4 — Добавление модуля аналогового ввода. Теперь давайте определим наш тег входного сигнала, предположим, что датчик давления может измерять давление от 0 до 10 бар и выдает соответствующий сигнал от 4 до 20 мА. Мы определим этот входной сигнал в первых тегах входного модуля. См. рисунок 5. Рисунок 5 — Определение тега входного сигнала. Как мы уже говорили, входной модуль может работать с различными входными сигналами, будь то 0–10 В или 4–20 мА, поэтому нам нужно назначить правильную конфигурацию для нашего датчика. Как мы уже говорили, сигнал давления подается в форме 4–20 мА, поэтому мы настроим наш входной канал на него. Смотрите рисунок 6. Рисунок 6 – Настройка входного канала Теперь, когда мы закончили часть конфигурации оборудования, мы начнем программировать наш код обработки. Для этого мы создадим функцию FC, чтобы мы могли повторно использовать ее каждый раз, когда у нас есть аналоговый сигнал для обработки. Внутри этого FC мы создадим логику, которая будет обрабатывать аналоговый сигнал и преобразовывать его в физическое измеренное значение. В TIA Portal есть предопределенные инструкции, которые мы можем использовать для этого, эти инструкции — инструкции NORM_X и SCALE_X. Смотрите рисунок 7. Рисунок 7 – Инструкции NORM_X и SCALE_X Как вы можете видеть, NORM_X нормализует аналоговый вход в значение от 0 до 1, а затем SCALE_X будет использоваться для масштабирования этого нормализованного значения в диапазоне измеренного физического значения, которое в случае нашего датчика составляет от 0 до 10 бар. Мы использовали функцию FC вместо того, чтобы писать наш код непосредственно в главном OB1, чтобы сделать наш код пригодным для повторного использования с любым аналоговым сигналом. Каждый раз, когда у меня есть новый аналоговый входной сигнал, я просто перетаскиваю блок FC в наш главный OB1 и просто записываю связанные параметры требуемого входа. Смотрите рисунок 8. Рисунок 8 – Перетащите свой FC. Когда вы перетаскиваете FC в свой главный OB1, вам будет предложено указать связанный параметр этого вызова функции. В нашем случае входной сигнал — это датчик давления, а ScaledMIN и ScaledMAX — это диапазон значений измерения 0–10 бар. Смотрите рисунок 9. Рисунок 9 — Назначение параметров функции нашему датчику давления. Если у меня есть новый аналоговый вход, то мне не придется заново создавать логику ПЛК, я просто перетащу FC в главный OB1 и назначу новые параметры датчика. Предположим, что теперь у нас есть новый аналоговый датчик для измерения уровня внутри резервуара с водой от 0 до 100 % резервуара. Мы выполним те же шаги, что и раньше, начав с определения нового входного тега. Смотрите рисунок 10. Рисунок 10 — Определение нового датчика уровня Далее мы настроим входной канал для датчика уровня, как на рисунке 6. Мы предположим ту же конфигурацию. Далее мы просто перетащим созданный нами FC и просто назначим параметры датчика уровня. Смотрите рисунок 11. Фото 11 – Повторное использование FC с датчиком уровня. Как вы можете видеть на предыдущем рисунке, это одно из многих преимуществ использования функций FC в вашей логике, поскольку это помогло сократить объем программирования, который мы сделали. Теперь у вас есть универсальный код, который можно многократно использовать с любым входным аналоговым сигналом, который вам может понадобиться в вашем проекте ПЛК. Смотрите следующую симуляцию обработки входных сигналов в ПЛК Siemens. Аналоговые входы в S7-300 и S7-400 Чтобы увидеть, как мы обрабатываем аналоговые сигналы в старых ПЛК семейства S7, таких как S7-300, давайте начнем с создания нового проекта и добавления ЦП S7-300. Выбранный ПЛК уже имеет достаточно каналов аналогового ввода, поэтому мы не будем добавлять аналоговые модули. См. рисунок 12. Фото 12 — Добавление ПЛК S7-300. Затем мы определим новый тег аналогового датчика, предположим, что это датчик давления с диапазоном измерения от 0 до 100 бар и выходом 4–20 мА. Мы настроим входной канал ПЛК, как мы делали это ранее с S7-1200, чтобы он соответствовал нашему датчику аналогового ввода. См. рисунок 13. Фото 13 — Настройте входной канал. Теперь к части кодирования ПЛК: инструкция в s7-300, которая используется для обработки аналоговых сигналов, отличается от s7-1200. В ПЛК S7-1200 мы должны использовать NORM_X и SCALE_X. но в S7-300 у нас нет нормализованной инструкции, используется только инструкция SCALE. Смотрите рисунок 14. Рисунок 14 – Инструкция SCALE в S7-300 Как вы можете видеть на предыдущем рисунке, инструкция SCALE в S7-300 в некотором роде похожа на инструкции NORM_X и SCALE_X, объединенные вместе. Есть еще одно явное отличие, а именно вход BIPOLAR. Вход BIPOLAR используется для указания того, следует ли интерпретировать значение параметра IN как биполярное или униполярное. Параметр может принимать следующие значения: BIPOLAR = 1, тогда предполагается, что входное целочисленное значение находится в диапазоне от -27648 до +27648. Например, когда аналоговый датчик выдает нам выходной сигнал в диапазоне от -10 В до +10 В BIPOLAR = 0, то предполагается, что входное целочисленное значение находится в диапазоне от 0 до 27648. Например, когда датчик выдает нам выходной сигнал в диапазоне 0-10 В И это просто как обрабатывать аналоговые входные сигналы в ПЛК S7-1200 и S7-300. Что лучше для управления? — Аналоговые или цифровые сигналы Послушайте, оба сигнала важны и полезны для любой системы автоматизации, но я лично предпочитаю использовать аналоговые сигналы, если могу, потому что наличие аналоговых сигналов измерений для физических величин процесса даст мне непрерывный мониторинг параметров процесса, что позволит мне лучше отслеживать и контролировать мой процесс. Кроме того, наличие непрерывного мониторинга параметров позволит мне устанавливать различную логику управления для различных значений сигнала, это упростит наличие диапазона значений для управления процессом и других диапазонов значений для аварийных сигналов и предупреждений об отклонении процесса от нормальной работы. Заключение Аналоговый сигнал — это непрерывное представление физической величины в вашей системе. Аналоговые входы чаще всего предоставляются в диапазоне 0–10 В или 4–20 мА. Аналоговая обработка сигнала означает преобразование аналогового сигнала 4–20 мА в диапазон значений, который соответствует реальной физической величине и который может понять ПЛК. В современном семействе ПЛК S7, например S7-1200, обработка аналоговых сигналов выполняется с помощью инструкций NORM_X и SCALE_X. В более старом семействе ПЛК S7, например S7-300, обработка аналоговых сигналов выполняется с помощью инструкции SCALE, которая по сути является комбинацией инструкций NORM_X и SCALE_X. -
Как получить резервную копию программы с физического ПЛК Siemens?
leizuofa posted A plc and hmi russian article in PLC programming learning
В этой статье мы покажем, как сделать резервную копию программы с физического ПЛК на ваш компьютер с помощью программного обеспечения портала Siemens Tia. Содержание: Зачем вам может понадобиться сделать резервную копию? Как сделать резервную копию с ПЛК? Заметки о резервном копировании с ПЛК Заключение Зачем вам может понадобиться сделать резервную копию? Представьте, что вы случайно удалили свое программное обеспечение с ПК во время работы с ним. Или, может быть, вам нужно сделать обновление определенного программного обеспечения процесса, которое работает уже 10 лет, и у вас больше нет программного кода. Вместо того, чтобы переписывать весь код с нуля, будет проще просто загрузить текущий код и внести в него свои изменения. В этой статье мы покажем, как легко загрузить программное обеспечение, содержащееся внутри ПЛК, на ваш ПК. Как сделать резервную копию с ПЛК? TIA Portal с новыми контроллерами Siemens S7-1200 и S7-1500 обеспечивает больше преимуществ при создании резервной копии по сравнению с ними, когда вы работаете со старыми контроллерами, такими как S7-300 или S7-400, со старыми контроллерами вы создадите резервную копию, но она не будет отображать никаких комментариев или деталей адресации, программное обеспечение будет работать нормально, но его будет трудно читать или понимать. С новыми контроллерами ПЛК вы теперь можете загружать как код, так и все связанные с ним адресации и комментарии, что значительно упростит чтение кода и сделает возможными любые его обновления. Шаги по загрузке программного обеспечения из ПЛК Создайте новый проект, но в отличие от того, что мы делаем обычно, мы не будем добавлять новое устройство, а нажмем «Онлайн» и выберем «загрузить устройство как новую станцию». См. рисунок 1. Рисунок 1 — Загрузите устройство как новую станцию. Это позволит вам загрузить устройство в окно PG/PC. См. рисунок 2. Рисунок 2 – Окно загрузки устройства. Вам нужно выбрать тип интерфейса PG/PC, как показано на последнем рисунке, а затем нажать «Начать поиск». После завершения поиска вы увидите все устройства, которые были найдены вашим программным обеспечением. Обратите внимание, что не обязательно искать только ПЛК; вы также сможете найти HMI, модули ввода-вывода и все остальные модули связи, которые может обнаружить программное обеспечение. См. рисунок 3. Рисунок 3 – Сканирование завершено и устройства найдены. После завершения сканирования вы можете выбрать ПЛК, который необходимо загрузить, а затем нажать «Загрузить». Это начнет загрузку программного обеспечения с ПЛК на ваш портал TIA. См. рисунок 4. Рисунок 4 – Загрузка с ПЛК завершена. Как вы можете видеть на предыдущем рисунке, весь проект, сохраненный на ПЛК, будет загружен на ваш портал TIA. Даже со всеми комментариями и адресами. Смотрите рисунок 5. Рисунок 5 — Проект ПЛК загружен Как вы можете видеть, весь проект ПЛК был загружен с ПЛК на ваш ПК. Со всеми блоками, комментариями и конфигурациями проекта. Заметки о резервном копировании с ПЛК Если у вашего ПК и ПЛК разные IP-адреса, портал TIA попросит вас назначить новый IP-адрес для вашего ПК, который соответствует адресации ПЛК, и даже сделает это автоматически, если вы разрешите. Если проект на ПЛК защищен паролем, вам будет предложено ввести этот пароль перед началом загрузки, если вы не сможете указать правильный пароль, загрузка не начнется. Убедитесь, что вы знаете этот пароль, если он есть. Иногда TIA Portal находит ваш ПЛК, но не может загрузить проект по разным причинам, например, проект на ПЛК написан в версии TIA Portal, отличной от той, которую вы используете сейчас. В любом случае вам будет показана причина неудачной загрузки, и вы сможете загрузить проект после устранения этих причин. Заключение Вы можете загрузить проект на ПЛК на свой ПК с помощью TIA Portal. Если ПЛК — s7-1200 или s7-1500, проект будет загружен со всеми соответствующими адресами и комментариями. Если есть какая-либо причина, по которой TIA Portal не может загрузить проект, эта причина будет показана вам TIA Portal, и вы сможете загрузить проект после устранения проблемы. -
Какой язык лучше всего подходит для программирования ПЛК?
leizuofa posted A plc and hmi russian article in PLC programming learning
Когда вы слышите о программировании ПЛК, пять используемых в нем языков — релейная логика, структурированный текст, функциональная блок-схема, последовательная блок-схема и список инструкций. Любой язык, если его понять, можно использовать для написания кода приложения и правильного управления машиной. Лучший язык программирования ПЛК Рисунок — пример релейной логики Но часто начинающие программисты ПЛК путаются, что использовать для написания программы. Если он понимает преимущества и недостатки языка, то он может легко определить, что использовать для написания программы ПЛК. Поэтому необходимо понимать разницу между ними и определить, какой язык использовать для кодирования. В этой статье мы рассмотрим, какой язык лучше всего подходит для программирования ПЛК. Релейная логика Релейная логика — это самый базовый тип языка программирования ПЛК. Его можно легко соотнести со схемой управления электропроводкой. Традиционно для управления выходами в соответствии с предоставленными входами использовалась электрическая проводка управления. Схема релейной логики, состоящая из контактов и катушек, была реализована таким же образом в программировании релейной логики. У вас есть ряд ступеней, каждая из которых имеет контакты и катушки. Когда ступень включена, катушка, в зависимости от ее типа, работает соответствующим образом. Вы можете написать столько ступеней в программе, сколько необходимо, и код будет выполняться соответствующим образом. Когда вы видите это, сходство похоже на лестницу, и поэтому название дано релейной логикой. Обратитесь к схеме ниже для понимания. Вы можете увидеть, насколько это просто. На приведенной выше иллюстрации входы, связанные с коммутационным устройством в релейной логической схеме, показаны как контакты в релейной логической схеме. Выходная катушка M1 в релейной логической схеме представлена символом выходной катушки в релейной логической схеме. Номера адресов, появляющиеся над каждым символом контакта/катушки на лестничной диаграмме, являются ссылками на расположение внешних входных/выходных соединений с логическим контроллером. Таким образом, между двумя конечными шинами питания вы можете разместить требуемые элементы и записать в них логику. Ступени выполняются циклически сверху вниз. Структурированный текст Структурированный текст можно назвать языком локального уровня ИТ. Сходство языка структурированного текста очень похоже на коды, которые мы пишем на языке программного обеспечения. Как следует из названия, структурированный текст представляет собой серию текстов, написанных способом присваивания. Инструкции должны заканчиваться точкой с запятой. Когда выполняется присваивание, текущее значение переменной с одним или несколькими элементами заменяется результатом вычисления выражения. Назначение состоит из спецификации переменной с левой стороны, за которой следует оператор присваивания: =, за которым следует выражение для вычисления. Обе переменные (левая и правая стороны оператора присваивания) должны иметь одинаковый тип данных. Для понимания обратитесь к приведенной ниже схеме. Как вы можете видеть, он имеет различные типы операций и условий. В приведенном выше примере оператор if-else используется для оценки выражения. Если условие истинно, то переменная, назначенная на выходной стороне, включается, а когда условие становится ложным, то переменная выключается. Таким образом, язык ST лучше всего подходит для математических вычислений, так как он выглядит трезвым и простым для понимания. Последовательная блок-схема Последовательная блок-схема — это самый продвинутый инструмент, когда вы хотите писать сложные программы повторяющимся или последовательным способом. Как следует из названия, язык SFC позволяет вам писать программу с помощью блок-схемы. Он работает по шагам, ветвям, ссылкам, переходам и переходам. Раздел SFC — это «машина состояний», т. е. состояние создается активным шагом, а переходы передают поведение переключения/изменения. Шаги и переходы связаны друг с другом посредством направленных ссылок. Два шага никогда не могут быть связаны напрямую и всегда должны быть разделены переходом. Процессы состояния активного сигнала происходят вдоль направленных связей и запускаются переключением перехода. Для понимания см. изображение ниже. Направление процесса цепочки следует направленным связям и проходит от конца предыдущего шага до начала следующего шага. Ветви обрабатываются слева направо. Каждый шаг имеет ноль или более действий. Условие перехода необходимо для каждого перехода. Последний переход в цепочке всегда связан с другим шагом в цепочке (через графическую связь или символ перехода) для создания замкнутого цикла. Поэтому цепочки шагов обрабатываются циклически. Функциональная блок-схема Язык функциональной блок-схемы (FBD), который обычно используется в микропроцессорах, также доступен в аналогичном формате в программировании ПЛК. Это схема блоков, связанных друг с другом, причем каждый блок имеет свой вход и выход. Язык FBD очень прост в устранении неполадок, поскольку вы можете буквально просмотреть весь код в одном представлении, а не прокручивать его вверх и вниз. Это помогает в быстром обслуживании и также повышает эффективность программирования. Для понимания обратитесь к изображению ниже. Как вы можете видеть, вы можете легко соединять различные типы функций и блоков линиями, что показывает, как поток происходит в логике. Вам просто нужно назначить входные и выходные контакты, соединить линии между этими контактами, и ваш код будет работать соответствующим образом. Список инструкций Программа, написанная на языке списка инструкций, состоит из ряда инструкций, которые последовательно выполняются логическим контроллером. Каждая инструкция представлена одной строкой программы и состоит из следующих компонентов: номер строки, текущее значение, которое можно увидеть только онлайн, оператор инструкции и операнд. Для понимания обратитесь к изображению ниже. Вы можете видеть, что каждая строка выполняет только одну операцию. Вместо контактов и катушек, используемых в релейной логике, у вас есть соответствующие инструкции загрузки и установки/сброса. Это смесь релейной логики и структурированного текста. Вот почему его также называют похожим на язык ассемблера. Когда вы подключаетесь к ПЛК онлайн, вы можете видеть анимированные значения в этом окне. Когда мы видим эти пять языков, мы видим, что большинство из них, которые обычно используются программистами, — это релейная логика, структурированный текст и функциональная блок-схема. У каждого языка есть свои достоинства и недостатки. Но эти три языка просты для понимания, интерпретации и проектирования. Это помогает программисту правильно проектировать логику. Это не значит, что оставшиеся два языка не используются. То, что он должен использовать для реализации кода, зависит от навыков программиста. Поэтому сложно прокомментировать лучший язык; но да, из этих трех также наиболее используемым является релейная логика. -
Разница между таймером и счетчиком – основы ПЛК
leizuofa posted A plc and hmi russian article in PLC programming learning
При разработке логики ПЛК вам всегда нужны таймеры и счетчики. Любой цикл в процессе автоматизации, как правило, неполный без использования таймеров и счетчиков. Они нужны вам для выполнения задачи по истечении определенного времени или для поддержания задачи включенной/выключенной в течение определенного времени. Их использование зависит от разрабатываемого приложения. И, прежде чем углубляться в расширенные инструкции ПЛК, программист должен сначала понять эти базовые блоки, чтобы правильно их реализовать и получить помощь в более легком изучении расширенных блоков. В этой статье мы узнаем разницу между таймерами и счетчиками в программировании ПЛК. Что такое таймер? Таймер — это инструкция, которая используется для включения или выключения выхода после определенной задержки. Например, если вы хотите включить лампу через 5 секунд, то используйте таймер для выполнения этой задачи. Таймер принимает вход, и когда вход включается, начинается его отсчет времени. По истечении 5 секунд включится выход таймера, который косвенно включит лампу. Мы говорим об обычном таймере этого типа. У таймера есть еще два типа — таймер выключения и импульсный таймер. Короче говоря, основная функция та же — выполнить задачу после определенной задержки. См. изображение выше для более правильного понимания. У таймера есть четыре входа и выхода — вход, заданное значение, текущее значение и выход. Вход принимает условие для запуска таймера, заданное значение используется для получения заданного значения таймера, текущее значение показывает текущее значение таймера, а выход используется для включения или выключения подключенной к нему переменной. Когда таймер ПЛК получает вход и если заданное значение равно 5 секундам, таймер запускается как 1, 2 и 3 и так далее до 5. Когда 5 секунд истекли, выход включается. Когда вход отключается, текущее значение таймера немедленно становится равным нулю. Независимо от того, работал ли таймер или нет; если вход отключен, то таймер не запустится, а его выход и текущее значение будут равны нулю. Это работа таймера TON (таймер с задержкой включения). Что такое счетчик? Счетчик — это инструкция, которая используется для включения выхода после достижения установленного счетчика. Счет может либо увеличиваться, либо уменьшаться. Например, если вы хотите включить лампу после нажатия кнопки пять раз, то используйте счетчик для выполнения этой задачи. Счетчик будет принимать вход, и когда вход включится, его счет увеличится до 1. Когда вход отключится, ничего не произойдет. Когда он снова получит вход, счет увеличится до 2. После того, как счет 5 истечет, тогда включится выход счетчика, который косвенно включит лампу. Это мы говорим о типе счетчика вверх. У счетчика есть еще один тип — счетчик вниз. Короче говоря, основная функция та же — выполнить задачу после определенного счета. См. изображение выше для более правильного понимания. У счетчика есть пять входов и выходов — вход счета, вход сброса, установленное значение, текущее значение и выход. Вход счета принимает условие для подсчета, вход сброса принимает условие для сброса счетчика, установленное значение используется для получения установленного значения счетчика, текущее значение показывает текущее значение счетчика, а выход используется для включения или выключения переменной, подключенной к нему. Когда счетчик получает вход счета и если установленное значение равно 5, счетчик увеличивается на 1 и так далее до 5; при получении каждого импульса на входе счета (это означает, что вход счета должен быть включен и выключен 5 раз). Когда 5 счетов будут завершены, выход включается. Теперь, даже если подан импульс входа счета, счетчик продолжит увеличиваться после 5, и выход также останется включенным. Чтобы снова вернуть счетчик в нулевое состояние, необходимо подать вход сброса. При подаче этого входа текущее значение счетчика становится нулевым, а выход также отключается. Таким образом, это похоже на работу с фиксацией. Чтобы снять фиксацию счетчика, необходимо сбросить его. Это работа счетчика CTU (счет вверх). Разница между таймером и счетчиком Основные различия между таймерами и счетчиками в ПЛК заключаются в следующем. Таймеру необходимо иметь свой вход непрерывно для включения переменной, но счетчику не нужно иметь свой вход непрерывно. Таким образом, таймер работает в непрерывных условиях, тогда как счетчик работает в импульсных условиях. Если вход таймера удален, то его выход вернется в нулевое состояние; но если вход счетчика удален, то счетчик сохранит свое последнее значение. У таймера нет входа сброса, тогда как счетчику требуется вход сброса, чтобы вернуть счетчик в исходное состояние. Типы таймеров: включенный таймер, выключенный таймер и импульсный таймер. Типы счетчиков — счетчик вверх и счетчик вниз. Установленное значение таймера может быть в секундах, минутах или миллисекундах; но установленное значение счетчика — это фиксированное целое число. -
Разница между обычными счетчиками и быстрыми счетчиками — изучите ПЛК
leizuofa posted A plc and hmi russian article in PLC programming learning
Программирование ПЛК имеет много типов инструкций и операндов для выполнения логики. Одной из наиболее используемых инструкций является счетчик. Счетчик используется для подсчета чисел. Подсчет требуется для многих приложений; например, даже небольшая логика, такая как подсчет количества бутылок, пропущенных за минуту, требует счетчика. Если такому небольшому приложению нужен счетчик, то технологии автоматизации имеют в себе много более крупных типов логики, которые используют счетчики для использования. Таким образом, это важные типы инструкций, используемых в программировании ПЛК. Существуют две категории счетчиков — обычные счетчики и счетчики шагов. В этой статье мы узнаем разницу между обычными счетчиками и быстрыми счетчиками. Что такое обычный счетчик? В ПЛК нет официального термина, называемого обычным счетчиком. Это просто определение, используемое для отображения двух основных типов счетчиков — повышающий и понижающий. Как следует из названия, эти инструкции используются для подсчета чисел при подаче входного импульса. Предположим, у вас есть кнопка, и вы хотите посчитать, сколько раз она была нажата. Если вы понимаете, что мы пытаемся передать, нажатие означает, что она будет оставаться включенной, пока она нажата. Как только вы убираете ее, она выключается. Это означает, что это импульсный вход, и счетчик понимает только такие типы входов. Если вход остается постоянно включенным, то он не будет считать. Он считает только тогда, когда вход переходит из состояния «включено» в состояние «выключено», а затем снова повторяет ту же последовательность. См. изображение выше для понимания. Вход CU (count up) используется для увеличения счетчика при каждом получении входного сигнала. Поскольку это триггер, счет увеличивается при получении входного сигнала импульсного типа. Вход PV — это установленное значение. Пока установленные счетчики не достигнуты, выход счетчика (Q) будет оставаться выключенным. Когда установленное значение достигнуто, выход включается. Теперь, даже если задан входной сигнал счета, счет будет продолжать увеличиваться, а выход останется включенным. Чтобы выключить его, необходимо подать вход сброса, который сбрасывает счетчик и делает текущее значение нулевым. Это общая работа счетчика. Что такое быстрый счетчик? Быстрый счетчик такой же, как и обычный счетчик, но единственное отличие в том, что он считает очень быстрые типы входов. Предположим, у вас есть датчик приближения, который включается или выключается, например, 1000 раз за 30 секунд. Такие быстрые входы трудно обнаружить в обычном счетчике, так как у него меньшее время сканирования. Быстрый счетчик выполнит эту работу, быстро подсчитав количество импульсов, полученных на его входе. Подобно обычному счетчику, его выход включается после достижения установленного значения, и для сброса счетчика и отключения выхода требуется вход сброса. Быстрый счетчик может работать на частотах 5 кГц. Поскольку функциональные блоки быстрого счетчика управляются определенными аппаратными прерываниями, поддержание максимальной частоты дискретизации может различаться в зависимости от вашего конкретного приложения и конфигурации оборудования. Не все входы ПЛК можно использовать в качестве быстрых счетчиков; у него есть только несколько выделенных входов ПЛК для назначения функции быстрого счета. Как видите, единственное различие между этими двумя счетчиками — это скорость работы, поскольку обычный счетчик не может принимать быстрый тип ввода. -
MITSUBISHI-RU Программирование и моделирование автоматической работы двери ПЛК
leizuofa posted A plc and hmi russian article in PLC programming learning
В этой программе ПЛК автоматическая работа двери разработана с использованием программирования ПЛК для открытия или закрытия двери при обнаружении объекта. Здесь объектом является не что иное, как автомобиль. Автоматическая работа двери Нижеприведенная симуляция показывает работу автоматической системы дверей. Входы и выходы Тип Номер устройства Название устройства Операция Вход X0 Нижний предел ВКЛ., когда дверь достигает нижнего предела. Вход X1 Верхний предел ВКЛ., когда дверь достигает верхнего предела. Вход X2 Датчик входных ворот ВКЛ., когда объект приближается к двери. Вход X3 Датчик выходных ворот ВКЛ., когда объект покидает дверь. Вход YO Дверь вверх Двигается вверх, когда YO ВКЛ. Выход Y1 Дверь вниз Двигается вниз, когда Y1 ВКЛ. Выход Y6 Свет горит, когда Y6 ВКЛ. Выход Y7 Зуммер Звучит, когда Y7 ВКЛ. (Лампа на экране горит). Описание программы Когда автомобиль приближается к входу, дверь поднимается. Датчик In-gate X2 используется для обнаружения присутствия автомобиля у входа. В момент проезда автомобиля дверь опускается. Датчик Out-gate X3 используется для обнаружения присутствия автомобиля после пересечения двери. Движение двери вверх останавливается, когда активируется верхний концевой выключатель (X1). Аналогично, движение двери вниз останавливается, когда активируется нижний концевой выключатель (X0). Дверь остается поднятой до тех пор, пока автомобиль обнаруживается в пределах диапазона входа (датчик In gate X2) и выхода (датчик Out X3). Зуммер (Y7) издает звуковой сигнал в качестве сигнала о движении двери. Пока автомобиль находится в пределах диапазона обнаружения, между датчиком In gate (X2) и датчиком Out (X3) горит свет (Y6). Состояние движения двери отображается включением или выключением четырех индикаторных ламп на панели управления. Возможно ручное управление дверью. Кнопки на панели управления можно нажимать, чтобы открыть (⬆Дверь вверх) или закрыть (⬇Дверь вниз) дверь. Программирование ПЛК -
MITSUBISHI-RU Программирование ПЛК сортировочной и распределительной линии – Расширенная логика
leizuofa posted A plc and hmi russian article in PLC programming learning
В этой расширенной логике ПЛК определяются различные размеры деталей и сортируются по размерам коробок, а затем размещаются в лотках. Детали представляют собой не что иное, как коробки разного размера, такие как маленькие, средние и большие. Робот размещает коробки разного размера в случайном порядке на конвейере. Затем система определяет размер коробки, перемещается к соответствующему конвейеру и размещает их в соответствующих лотках. Программирование ПЛК сортировочной и распределительной линии Нижеприведенная симуляция показывает работу системы сортировочной и распределительной линии. Входы и выходы Тип Номер устройства Название устройства Операция Вход X0 Начальная точка (Подача) ВКЛ. при обнаружении детали. Вход X1 Верхний ВКЛ. при обнаружении детали. Вход X2 Средний ВКЛ. при обнаружении детали. Вход X3 Нижний ВКЛ. при обнаружении детали на правом конце. Вход X4 Датчик ВКЛ. при обнаружении детали на правом конце. Вход X5 Датчик Конвейер движется вперед, когда Y1 ВКЛ. Вход X6 Обнаружение детали ВКЛ, когда деталь обнаружена перед толкателем. Вход X10 Начальная точка (выгрузка) ВКЛ, когда разгрузочный робот находится в начальной точке. Вход X11 Деталь на столе ВКЛ, когда деталь находится на столе. Вход X12 Работа робота завершена ВКЛ, когда работа робота завершена. Выход Y1 Конвейер вперед Конвейер движется вперед, когда Y2 ВКЛ. Выход Y2 Конвейер вперед Движется вперед, когда Y3 ВКЛ. Выход Y3 Крыло сортировки Конвейер движется вперед, когда Y4 ВКЛ. Выход Y4 Конвейер вперед Конвейер движется вперед, когда Y5 ВКЛ. Выход Y5 Конвейер вперед Выдвигается, когда Y6 ВКЛ и втягивается, когда Y6 ВЫКЛ. Толкатель не может быть остановлен в середине хода. Выход Y6 Толкатель Робот перемещает деталь в лоток, когда Y7 ВКЛ. Начинается цикл обработки. Выход Y7 Команда выгрузки Робот перемещает деталь в лоток, когда Y7 включен. Начинается цикл обработки. Выход Y10 Красный Горит, когда Y10 включен. Выход Y11 Зеленый Горит, когда Y11 включен. Выход Y12 Желтый Горит, когда Y12 включен. Описание программы Нажатие кнопки PB1 (X20) на панели управления запускает команду подачи (Y0), тем самым приводя робота в движение для перемещения объекта. После того, как робот выполнил свою задачу по перемещению детали и возврату в исходное положение, команда подачи (Y0) деактивируется. Активация команды подачи (Y0) заставляет робота поставлять деталь. Активация переключателя SW1 (X24) на панели управления запускает конвейеры для движения вперед. И наоборот, деактивация переключателя приводит к остановке конвейеров. Детали разных размеров, перемещаемые конвейером, а именно большие, средние и маленькие, сортируются по входным данным с верхнего (X1), среднего (X2) и нижнего (X3) датчиков и доставляются в назначенные лотки. Крупные детали направляются на задний конвейер, когда активируется сортировочное крыло (Y3) на разделенном конвейере, за которым следует деталь, транспортируемая на конвейере и в конечном итоге спускающаяся с правого края. Средние детали направляются на передний конвейер, когда сортировочное крыло (Y3) на разделенном конвейере деактивируется, и затем робот переносит их на лоток. Мелкие детали направляются на задний конвейер при активации сортировочного крыла (Y3) на разделенном конвейере. После активации датчика обнаружения детали (X6) на разделенном конвейере конвейер останавливается, и деталь подталкивается на лоток. Когда робот обнаруживает деталь на столе (X11), активируется команда «Выгрузить» (Y7). После того, как робот завершает свою работу, что обозначается включением статуса Robot operation done (X12) (что происходит, когда деталь укладывается на лоток), команда Unload (Y7) деактивируется. При условии, что переключатель SW2 (X25) на панели управления остается активированным, автоматическая подача новой детали происходит при следующих условиях: Когда робот начинает транспортировку средней детали. Когда в лоток добавляется небольшая деталь или большая деталь спускается с правого края конвейера. Индикаторы дисплея мигают следующим образом: Красный индикатор указывает на то, что робот находится в процессе подачи детали. Зеленый индикатор означает, что конвейер находится в движении. Желтый индикатор горит, когда конвейер стоит. Программа ПЛК -
MITSUBISHI-RU Программирование ПЛК сортировка и распределение коробок по высоте
leizuofa posted A plc and hmi russian article in PLC programming learning
В этом программировании ПЛК мы сортируем и распределяем коробки по высоте в назначенные складские отсеки с помощью датчиков и конвейеров. Эта программа ПЛК распределяет указанное количество деталей в соответствии с их размером. Сортировка коробок ПЛК по высоте Приведенная ниже симуляция показывает принцип работы логики ПЛК для сортировки коробок по высоте. Здесь у нас есть 3 разных размера коробок: маленькие, средние и большие. Для каждого размера коробок есть три складских отсека. Есть три толкателя и три конвейера. Для каждого размера коробок есть один толкатель и один конвейер. Робот размещает коробки на конвейере случайным образом. Датчики используются для определения размера коробки. Конвейеры запускаются и останавливаются, когда коробка соответствующего размера достигает их с помощью датчиков. Соответствующий толкатель активируется и перемещает коробку соответствующего размера в назначенные складские отсеки. Список входов/выходов ПЛК В таблице ниже перечислены входы и выходы этой системы. Тип Номер устройства Имя устройства Операция Вход X0 Начальная точка ВКЛ, когда робот находится в начальной точке. Вход X1 Верхний ВКЛ, когда обнаружена деталь. Вход X2 Средний ВКЛ, когда обнаружена деталь. Вход X3 Нижний ВКЛ, когда обнаружена деталь. Вход X4 Датчик ВКЛ, когда деталь обнаружена на наклонной поверхности. Вход X5 Датчик ВКЛ, когда деталь обнаружена на наклонной поверхности. Вход X6 Датчик ВКЛ, когда деталь обнаружена на наклонной поверхности. Вход X7 Датчик ВКЛ, когда деталь обнаружена на правом конце. Вход X10 Обнаружение детали ВКЛ, когда деталь обнаружена перед толкателем. Вход X11 Обнаружение детали ВКЛ, когда деталь обнаружена перед толкателем. Вход X12 Обнаружение детали ВКЛ, когда деталь обнаружена перед толкателем. Выход Y0 Команда подачи Одна деталь подается, когда Y0 ВКЛ. Начинается цикл процесса: Деревянная деталь повторяется в порядке M, S, L, M, M, L, S, S, L, L. Выход Y1 Конвейер вперед Конвейер движется вперед, когда Y1 включен. Выход Y2 Конвейер вперед Конвейер движется вперед, когда Y2 включен. Выход Y3 Конвейер вперед Конвейер движется вперед, когда Y3 включен. Выход Y4 Конвейер вперед Конвейер движется вперед, когда Y4 включен. Выход Y5 Толкатель Выдвигается, когда Y5 включен, и втягивается, когда Y5 выключен. Толкатель не может быть остановлен в середине хода. Выход Y6 Толкатель Выдвигается, когда Y6 включен, и втягивается, когда Y6 выключен. Толкатель не может быть остановлен в середине хода. Выход Y7 Толкатель Выдвигается, когда Y7 включен, и втягивается, когда Y7 выключен. Толкатель не может быть остановлен в середине хода. Описание программы Программирование программируемого логического контроллера (ПЛК) для сортировки коробок по высоте и распределению компонентов. Для запуска работы робота необходимо нажать кнопку PB1 (X20), расположенную на панели управления, которая активирует команду подачи робота (Y0). Команда подачи робота (Y0) деактивируется после того, как робот завершает перемещение детали и возвращается в исходное положение. Команда перемещения конвейера управляется переключателем SW1 (X24) на панели управления. Активация переключателя (включение) запускает движение конвейера вперед, а его деактивация (выключение) останавливает конвейер. Сортировка деталей, разделенных на большие, средние и маленькие размеры, выполняется с помощью входных данных от датчиков Верхний (X1), Средний (X2) и Нижний (X3). После сортировки детали транспортируются в предназначенные для них лотки. Наличие детали в толкателе определяется активацией (включением) датчиков обнаружения деталей (X10, X11 или X12). При обнаружении детали конвейер останавливается, а обнаруженная деталь перемещается на лоток. Примечание: работа толкателя регулируется командой активации толкателя. При получении сигнала ВКЛ толкатель полностью выдвигается, а сигнал ВЫКЛ заставляет толкатель втягиваться. Каждый лоток должен содержать определенное количество деталей в зависимости от их размера. Любые детали, превышающие указанные числа, обходят толкатель и выбрасываются с конвейера с правого конца. Назначенное количество деталей по размеру следующее: Большие: 3 детали Средние: 2 детали Маленькие: 2 детали ПЛК Ladder Logic -
Программа ПЛК для индикации аварийных сигналов в управлении процессами
leizuofa posted A plc and hmi russian article in PLC programming learning
Создайте программу ПЛК для индикации аварийных сигналов в отрасли управления процессами. Изучите программирование ПЛК на этом промышленном примере. Индикация аварийных сигналов в управлении процессами Во многих отраслях промышленности есть много машин, которые выполняют множество задач автоматически. В системе или процессе используется множество датчиков и компонентов. Иногда оператор не может определить проблемы машины или системы с помощью визуальных наблюдений. А также иногда есть вероятность, что машина перестанет работать из-за какой-то проблемы в ней. Схема проблемы Решение ПЛК Мы можем решить эту проблему, добавив аварийные сигналы в систему или процесс. Аварийные сигналы добавляются для оповещения оператора о необходимости отслеживать, что машина/процесс вот-вот перейдет свои предельные значения или уже перешел предел. Аварийные сигналы оператору сообщаются сигнализатором или гудками, а также разноцветными индикаторами на панели. (Например, зеленый свет означает «ОК», желтый означает «НЕ ОК», а красный означает «ПЛОХО».) Целью сигнализации является использование автоматизации для помощи операторам-людям в отслеживании и управлении процессами, а также оповещение их о нештатных ситуациях на предприятии. Входящие/входящие сигналы процесса постоянно отслеживаются, и если значение данного сигнала переходит в нештатное состояние, визуальный и/или звуковой сигнал тревоги информирует оператора о ситуации. Мы можем настроить сигналы тревоги для системы различными способами, такими как MIMIC, индикаторные лампы на панели управления, SCADA, HMI и т. д. Для обсуждения наших проблем мы рассмотрели одну простую систему и настроили сигналы тревоги для системы. Например, рассмотрим один процесс наполнения и выгрузки, и в этой системе мы хотим рассмотреть некоторые сигналы тревоги, мы будем отображать сигналы тревоги с помощью ламп на панели управления. Например, рассмотрим следующие сигналы тревоги для нашей системы: Нажата кнопка аварийного останова Ошибка открытия клапана подачи Ошибка закрытия клапана подачи Ошибка открытия выпускного клапана Ошибка закрытия выпускного клапана Здесь все ошибки, поэтому мы берем все красные цветовые обозначения, как показано на рисунке выше. Список входов и выходов в ПЛК Список входов НАЧАЛО цикла: I0.0 ОСТАНОВКА цикла: I0.1 Переключатель низкого уровня, LL: I0.2 Переключатель высокого уровня, LH: I0.3 Открытие VLV подачи LS: I0.4 Закрытие VLV подачи LS: I0.5 Открытие VLV диска LS: I0.6 Открытие VLV диска. VLV закрыть LS : I0.7 Аварийная остановка : I1.0 СБРОС : I1.1 Список выходов Цикл ВКЛ : Q0.0 Клапан подачи : Q0.1 Дисковый клапан : Q0.2 ЗУММЕР : Q0.3 Аварийная остановка нажата : Q0.4 (индикаторная лампа) Ошибка открытия VLV подачи : Q0.5 (индикаторная лампа) Ошибка закрытия VLV подачи : Q0.6 (индикаторная лампа) Ошибка открытия VLV диска : Q0.7 (индикаторная лампа) Ошибка закрытия VLV диска : Q1.0 (индикаторная лампа) Программа ПЛК для индикации аварийного сигнала в процессе Управление Объяснение логики В этом приложении мы использовали Siemens S7-300 PLC и программное обеспечение TIA Portal для программирования. Сеть 1: В сети 1 мы использовали схему фиксации для выхода цикла ВКЛ (Q0.0). Его можно запустить, нажав цикл START PB (I0.0) и STOP, нажав STOP PB (I0.1). Когда цикл будет START, система проверит уровень в баке. Если уровень в баке низкий, то начнется процесс подачи, а если уровень в баке достигнет высокого, то НАЧНЕТСЯ цикл выгрузки. Сеть 2: Когда уровень в баке достигает низкого значения, активируется LL (I0.2) и включается цикл подачи. Здесь мы взяли NC-контакт LH (I0.3), поэтому, когда ПЛК обнаружит высокий уровень, он ОСТАНОВИТ цикл подачи. Сеть 3: Когда уровень в баке достигает высокого значения, активируется LH (I0.3), и включается цикл выгрузки. Здесь мы взяли NC-контакт LL (I0.2), поэтому, когда ПЛК обнаружит низкий уровень, он ОСТАНОВИТ цикл выгрузки. Сеть 4: Когда система получает входной сигнал аварийного останова (I1.0), она активирует выходной сигнал аварийного останова (Q0.4), и оператору будет предоставлена индикация тревоги. Сеть 5: В этой сети мы настроили сигнализацию об ошибке открытия клапана подачи (Q0.5), когда клапан подачи включен, а клапан подачи открыт LS (I0.4), тогда таймер ЗАПУСТИТСЯ, и через 5 с включается сигнализация об ошибке открытия клапана подачи (Q0.5). Сеть 6: В этой сети мы настроили сигнализацию об ошибке закрытия клапана подачи (Q0.6), когда клапан подачи закрыт, а клапан подачи закрыт LS (I0.5), тогда таймер ЗАПУСТИТСЯ, и через 5 с включается сигнализация об ошибке закрытия клапана подачи (Q0.6). Сеть 7: В этой сети мы настроили сигнализацию об ошибке открытия клапана диска (Q0.7), когда клапан подачи включен, а клапан подачи открыт LS (I0.6), тогда таймер ЗАПУСТИТСЯ, и через 5 с включается сигнализация об ошибке открытия клапана диска (Q0.7). Сеть 8: В этой сети мы настроили сигнализацию об ошибке закрытия дискового VLV (Q1.0), когда дисковый клапан ЗАКРЫТ и не обнаружена LS-функция закрытия дискового VLV (I0.7), то запустится таймер, и через 5 с включится сигнализация об ошибке закрытия дискового VLV (Q1.0). Сеть 9: В этой сети мы настроили ЗУММЕР для всех сигналов тревоги, при обнаружении сигнала тревоги активируется ЗУММЕР (Q0.3), и его можно СБРОСИТЬ, нажав кнопку СБРОС (I1.1). Сеть 10: Оператор может сбросить ЗУММЕР, нажав RESET (I1.0) Тестовые случаи Примечание: приведенная выше логика ПЛК дает базовую идею о применении ПЛК в индикации аварийных сигналов процесса. Логика ограничена и не является полным приложением. -
Программа ПЛК для положительного фронта импульсного выхода для одного цикла сканирования
leizuofa posted A plc and hmi russian article in PLC programming learning
Это программа ПЛК для положительного фронта импульсного выхода для одного цикла сканирования. Изучите логику релейной связи с решением. Положительный фронт импульсного выхода Описание проблемы В некоторых приложениях нам нужно запустить операцию/функцию на основе внешнего входного сигнала. Мы можем использовать цифровой вход в качестве команды запуска для активации требуемой функции. Иногда мы используем положительный переход цифрового входного сигнала для запуска команды вместо непрерывного/полного импульса цифрового входного сигнала. Здесь мы рассмотрим пример простой логики, в которой два значения регистров будут увеличиваться после получения команды запуска. Каждый регистр имеет предустановленное значение, скажем, значение «1». Таким образом, при каждой команде запуска значения регистра сумматора будут увеличиваться на значение «1». Для регистра сумматора 1 мы используем положительный фронт (от 0 до 1) запускаемого входного сигнала, а для регистра сумматора 2 мы используем простой цифровой входной сигнал (от 0 до 1 и от 1 до 0). Мы видим преимущества и недостатки использования команды запуска с использованием положительного фронта и без него. Мы можем использовать ту же логику в других приложениях, например, обнуление значений регистра, принудительное назначение значениям регистра определенного значения с небольшим изменением логики и т. д. Проблема Решение Мы можем решить эти типы проблем с помощью положительного фронта или нарастающего фронта цифрового входа. Здесь мы рассмотрим ПЛК S7-300 для программирования, поэтому мы можем контролировать значение и моделировать его. Мы можем использовать SIM ПЛК для целей моделирования. Здесь мы рассмотрели один простой пример. В этом примере мы рассмотрим регистр «Администратор 1», который будет добавлять значение «1», когда происходит переход от 0 к 1 команды запуска. Значение регистра будет увеличиваться на значение 1 после каждого запуска. Для регистра «Администратор 2» значение будет увеличиваться после получения цифрового входа. Здесь мы не используем запуск по положительному фронту. Список входов/выходов Список входов Команда запуска: I0.0 Катушка памяти Положительный фронт команды запуска: M0.0 Общее значение: MW2 Общее значение 2: MW4 Логика ПЛК Сеть 1: Начальное значение регистра «Администратор 1» равно нулю. После подачи команды запуска по положительному фронту 18 раз выход будет иметь значение 18, поскольку он увеличивается на значение «1». Моделирование (PLCSIM-300) для команды запуска с положительным фронтом. Сеть 2: Начальное значение регистра «Администратор 2» равно нулю. После подачи команды запуска (без положительного/отрицательного фронта) 18 раз на выходе будет некоторое случайное число (например, 7506) вместо значения 18, как при непосредственном получении команды запуска. Моделирование (PLCSIM-300) для команды запуска без положительного фронта. Описание логики ПЛК В этом приложении мы использовали ПЛК Siemens S7-300 и программное обеспечение TIA Portal для программирования. Здесь мы рассмотрели два примера для объяснения положительного фронта. Любой может легко понять концепцию. В сети 1, когда срабатывает команда запуска (I0.0), то произойдет переход от 0 к 1, и будет выполнена инструкция положительного импульса. Скажем, регистр «Администратор 1» будет сохранен со значением «1» в MW0, если сработает команда запуска (I0.0), то значение будет увеличено на «1». Вот, например, мы сработали 18 раз, когда сумматор 1 равен нулю, поэтому сумматор добавил 18 в общее значение (MW0) Другой пример мы взяли в сети 2, не используя положительный импульс. Так что здесь вы можете увидеть результат. Скажем, мы нажали или сработали 18 раз, но это добавило 7506 (это случайное значение, оно может отличаться во время моделирования) в общее значение 2 (MW4), так что это не правильное сложение. Поскольку один импульс имеет восходящие или нисходящие фронты / положительные или отрицательные импульсы (от 0 до 1 и от 1 до 0). Здесь мы также использовали PLC SIM для моделирования, поэтому мы можем смоделировать общее сложение. В первой сети мы добавили положительный фронт, поэтому симулятор показывает 18. Во второй сети мы добавили команду триггера без положительного фронта, поэтому он показывает некоторое случайное значение. Это концепция положительного фронта, мы можем использовать этот положительный фронт во время любого приложения программирования. Вышеприведенная программа и моделирование предназначены только для пояснения, и значение моделирования может отличаться во время моделирования. Результат Примечание: Приведенная выше логика ПЛК дает базовую идею о применении команды запуска по положительному фронту в логике ПЛК. Логика ограничена и не является полным приложением. -
Программа ПЛК для автоматической системы отбраковки бутылок
leizuofa posted A plc and hmi russian article in PLC programming learning
Это программа ПЛК для автоматической системы отбраковки бутылок. Изучите логику релейной связи с помощью этого упражнения и решения ПЛК. Автоматическая отбраковка бутылок Описание проблемы В настоящее время автоматизация в промышленности необходима для точного и быстрого производства. Давайте рассмотрим пример компаний по производству бутылок для газировки, где ленточный конвейер используется для передачи бутылок с одной станции на другую. Но прежде чем бутылки попадут на станцию розлива газировки, необходимо привести все бутылки в вертикальное положение для дальнейшей обработки Упавшая бутылка на конвейере может создать проблему в следующем процессе. Поэтому здесь мы обсудим простую логику ПЛК, которая обрабатывает упавшую бутылку. Диаграмма проблемы ПЛК Решение проблемы ПЛК Итак, для этого мы используем систему ПЛК на станции розлива, которая отбраковывает упавшую бутылку с конвейера и расчищает путь для следующего процесса. Этот процесс выполняется с помощью датчиков и исполнительных механизмов. Мы используем пневматический поршневой цилиндр для сталкивания упавших бутылок с конвейера. Когда конвейер работает, все бутылки перемещаются с одной станции на другую для следующего процесса. Используются два датчика для обнаружения стоящих и упавших бутылок, один пневматический цилиндр для сталкивания упавшей бутылки с конвейера. Список входов/выходов Список входов Запуск PB: I0.1 Остановка PB: I0.0 Датчик X1: I0.2 Датчик X2: I0.3 Список выходов Цикл ВКЛ: Q0.0 Конвейер: Q0.1 Цилиндр: Q0.2 Программа ПЛК для автоматической системы отбраковки бутылок Пояснение программы ПЛК В этом приложении мы использовали ПЛК Siemens S7-1200 и программное обеспечение TIA Portal для программирования. Мы также можем разработать эту логику с помощью релейной цепи. Сеть 1: В сети 1 мы взяли условие цикла ВКЛ для машины. Здесь мы взяли START PB (I0.1) для запуска цикла и STOP PB (I0.1) для цикла ОСТАНОВКИ. Мы взяли параллельный выход конвейера (Q.1) с циклом ВКЛ (Q0.0), чтобы мы могли управлять конвейером с условием цикла ВКЛ. Сеть 2: В сети 2 мы взяли датчики X1(I0.2) и X2(I0.3) в качестве входов. Мы использовали НО контакт для датчика X2 (I0.3) и НЗ контакт для датчика X1 (I0.2). Когда бутылки перемещаются по конвейеру, эти датчики определяют положение бутылок, стоят они или упали. Датчик X2(I0.3) определяет нижнее положение бутылки, а датчик X1(I0.2) определяет верхнее положение бутылки. В ПЛК мы разработали схему, которая следует команде, что если датчик X2(I0.3) обнаруживает бутылку, а датчик X1(I0.2) не обнаруживает бутылку, то пневматический привод (Q0.2) сработает и отклонит бутылку от конвейера. После этого идеальные бутылки попадут на станцию розлива газировки, и весь цикл будет завершен. Результат Примечание: приведенная выше логика ПЛК дает базовую идею о применении ПЛК в системе автоматической обработки отбраковки бутылок. Логика ограничена и не является полным применением. -
Программа ПЛК для ежедневной записи производства
leizuofa posted A plc and hmi russian article in PLC programming learning
Программа ПЛК для ежедневной записи производства. Изучите описание проблемы с подробным объяснением релейной логики. Ежедневная запись производства Описание проблемы Во многих отраслях промышленности требуется подсчитывать количество продукции, произведенной за один день, и это очень необходимо для продажи продукции или отслеживания количества продукции на ежедневной основе. В старые времена для подсчета готовой продукции назначались операторы-люди, но из-за некоторых человеческих ошибок точный подсчет невозможен. Поэтому мы не можем получить правильный подсчет всех продуктов и не можем эффективно отслеживать количество продукции. В основном такие типы проблем возникают в пищевой промышленности и производстве напитков, в упаковочной промышленности, в приложениях для розлива в бутылки и т. д. Поэтому мы можем использовать простую логику на основе ПЛК для отслеживания ежедневного производства и его электронной регистрации. Схема проблемы Решение ПЛК Здесь мы решим проблему подсчета готовой продукции с помощью датчиков и программирования ПЛК. Первый датчик определяет продукт и подсчитывает количество, а значение будет показано на цифровом дисплее (как показано на рисунке выше). Для простого объяснения мы рассмотрим один простой пример системы подсчета пустых коробок. В этой системе пустые коробки перемещаются из первого процесса во второй процесс (например, из одного места в другое). Датчик используется для подсчета пустых коробок. Поэтому, когда датчик обнаружит пустую коробку, дисплей начнет отсчет, скажем, с 1, и это делается с помощью простой логики. Каждые 24 часа / через день мы можем сбросить значение счетчика с помощью кнопки RESET. Здесь мы рассмотрим две партии производства для простого объяснения. А также мы рассмотрели два указания завершения партий для оператора для каждой партии, которые будут отображаться на локальной панели. С помощью логики ПЛК мы реализуем желаемую логику. Таким образом, когда любая партия будет завершена, индикаторная лампа будет включена в соответствии с программой ПЛК. После того, как будет достигнута цель производства, счетчик дисплея можно сбросить с помощью кнопки RESET. Список входов/выходов Список входов Датчик детектора коробок: I0.0 Сброс: I0.1 Главный переключатель: I0.2 Список выходов Цель выполнена: Q0.0 Партия 1 выполнена: Q0.1 Партия 2 выполнена: Q0.2 Релейная диаграмма для ежедневной записи производства Описание программы ПЛК В этом приложении мы использовали ПЛК Siemens S7-1200 и программное обеспечение TIA Portal для программирования. Сеть 1: В сети 1 мы использовали главный переключатель (I0.2) для запуска системы/партии и использовали НО контакт датчика детектора коробок (I0.0) последовательно. Здесь мы рассмотрели один счетчик UP, поэтому, когда датчик детектора коробок (I0.0) обнаруживает коробку, счетчик начинает отсчет. Здесь мы также взяли выход завершения цели (Q0.0) для индикации завершения цели для индикации оператора на панели. Нажав кнопку RESET (I0.1), оператор может СБРОСИТЬ старую запись о производстве. Операция счетчика используется для подсчета продуктов, в которой RESET (I0.1) используется для сброса записи о производстве. А предустановленное значение (PV) составляет 20 продуктов. Значение счетчика (CV) равно MW2, что указывает на фактическое количество продуктов, обнаруженных датчиком, и это значение будет использоваться в следующих звеньях для отслеживания статуса партии. Сеть 2: В сети 2 мы использовали логику партии 1 с выхода блока счетчика CV. Здесь мы использовали компаратор для подсчета 10 коробок для партии 1, и когда он будет завершен, загорится лампа завершения партии 1 (Q0.1). В этом сложении равно равному компаратору, в котором вход равен (MW2) и для 10 продуктов. Сеть 3: В сети 3 мы использовали логику партии 1 с выхода блока счетчика CV. Здесь мы использовали компаратор для подсчета 20 коробок для партии 2, и когда она будет завершена, загорится лампа завершения партии 2 (Q0.2) И таким образом мы можем решить, сколько продуктов и партий произведено. Тестовые случаи во время выполнения Примечание: приведенная выше логика ПЛК дает базовую идею о применении ПЛК в записи промышленного производства. Логика ограничена и не является полным приложением. -
Программа ПЛК для процесса заполнения и слива воды
leizuofa posted A plc and hmi russian article in PLC programming learning
Это программа ПЛК для процесса заполнения и слива воды с использованием ПЛК S7-1200. Процесс заполнения и слива воды Описание проблемы Во многих отраслях промышленности или на заводах для хранения воды используется множество ручных систем заполнения водой. В ручной системе есть много недостатков, таких как точность, проблемы с задержкой по времени, потеря жидкости и затраты времени. И из-за ручной системы нам приходится назначать оператора для работы машины. Из-за ручной системы происходит потеря воды Здесь мы обсуждаем полуавтоматическую систему. Диаграмма Решение ПЛК Чтобы решить эту проблему, мы будем использовать ПЛК S7-1200 для программирования. Здесь мы используем два датчика для измерения уровня, один для высокого уровня, а второй для низкого уровня. Мы используем клапан подачи (MV1) для цикла заполнения бака и клапан сброса (MV2) для цикла опорожнения бака. Оба будут контролироваться в соответствии с логикой датчика. Таким образом, когда уровень воды опускается ниже нижнего уровня, клапан подачи автоматически включается, а когда уровень воды достигает высокого уровня и это определяется датчиком высокого уровня, процесс опорожнения включается автоматически. При обнаружении высокого уровня включается зуммер для подачи сигнала тревоги. Цикл останавливается, если пользователь нажимает кнопку остановки на панели управления. Входы и выходы ПЛК Цифровые входы Пуск PB: I0.0 Останов PB: I0.1 TLB 1: I0.3 TLB 2: I0.2 Цифровые выходы Цикл ВКЛ: Q0.0 Клапан MV1 (подача): Q0.1 Клапан MV2 (выгрузка): Q0.2 Мешалка/миксер M: Q0.3 Зуммер: Q0.4 ПЛК Процесс заполнения и выгрузки воды Пояснение программы ПЛК Для этого приложения мы использовали ПЛК S7-1200 и программное обеспечение портала TIA для программирования. В сети 1 мы использовали схему фиксации для выхода цикла ВКЛ (Q0.0). Его можно запустить, нажав ПУСК PB (I0.0), и остановить, нажав СТОП PB (I0.1). Когда цикл будет запущен, система проверит уровень в баке. Если уровень в баке низкий, то начнется процесс подачи, а уровень в баке высокий, то начнется цикл выгрузки. Здесь мы взяли НО контакт для обоих датчиков в программе для простоты. Это можно сделать с помощью релейной логики в полевых условиях или вы можете использовать такой тип датчиков. Когда бак обнаружит низкий уровень, то TLB 2 (I0.2) будет активирован, и тогда цикл подачи будет включен. Здесь мы взяли НЗ контакт TLB1 (I0.3), поэтому, когда ПЛК обнаружит высокий уровень, то он остановит цикл подачи. Когда бак обнаружит высокий уровень, то TLB 1 (I0.3) будет активирован, и тогда цикл выгрузки будет включен. Здесь мы взяли НЗ контакт TLB2 (I0.2), поэтому, когда ПЛК обнаружит низкий уровень, то он остановит цикл выгрузки. Смеситель M (Q0.3) должен быть включен во время цикла выгрузки для смешивания. Здесь мы также рассмотрели сигнализацию для высокого уровня, чтобы информировать оператора. При обнаружении TLB 1(I0.3) активируется зуммер (Q0.4). Во время всех функций цикл должен быть включен. Тестовые случаи во время выполнения Примечание: приведенная выше логика ПЛК обеспечивает базовую идею о применении ПЛК в процессе заполнения и слива воды. Логика ограничена и не является полным приложением.